How real-time tool tracking reduced downtime and cut costs
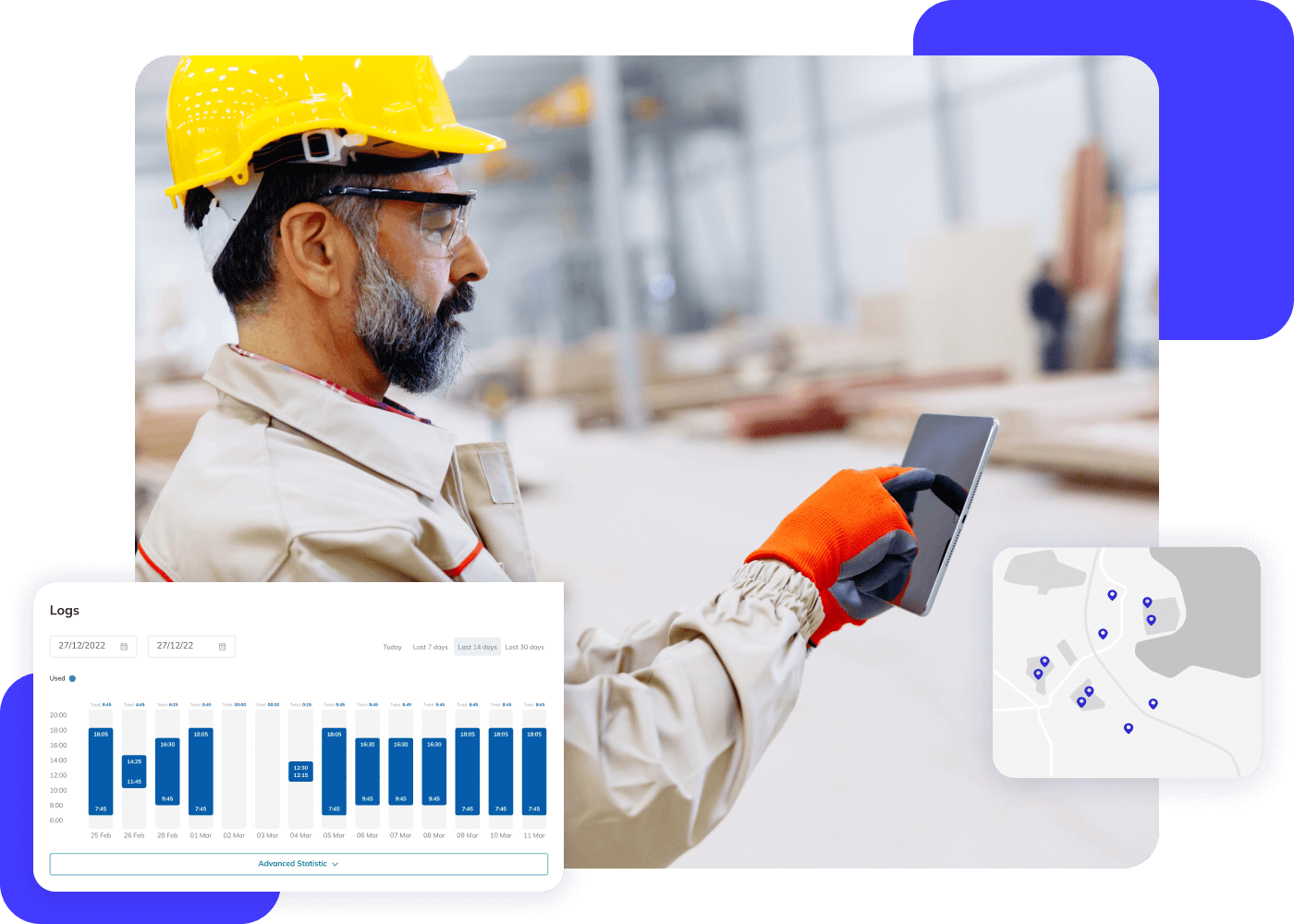
Problem
Clint’s crews frequently experienced downtime due to missing or unavailable tools, impacting productivity. Workers had to wait for tools to be delivered from remote warehouses or, in some cases, purchase new ones, increasing both downtime and logistics costs.
Solution
The company implemented a tool tracking system to monitor tool availability and activity in real-time. This enabled workers to request tools from neighboring crews when they weren’t in use, reducing dependency on distant storage facilities or new purchases/ tool rentals.
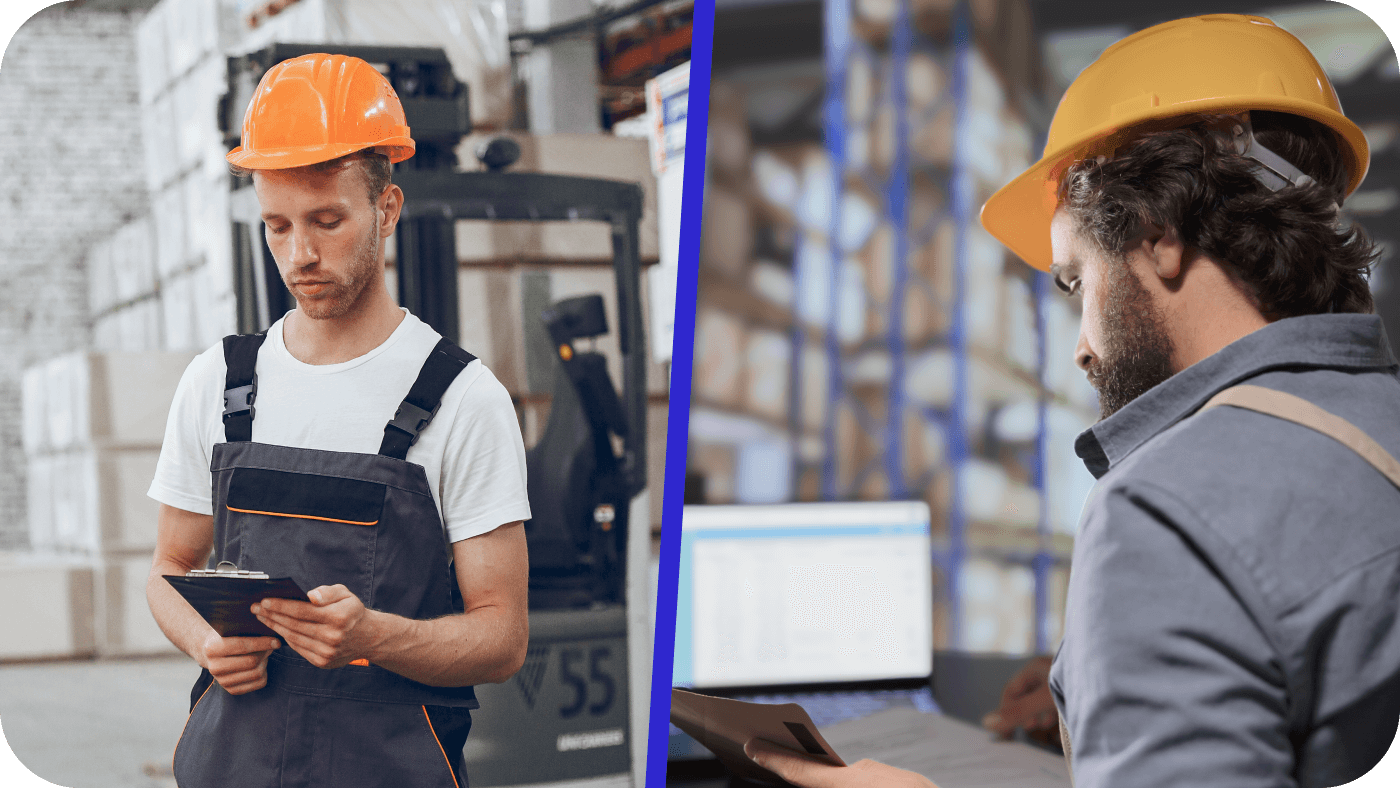
Result
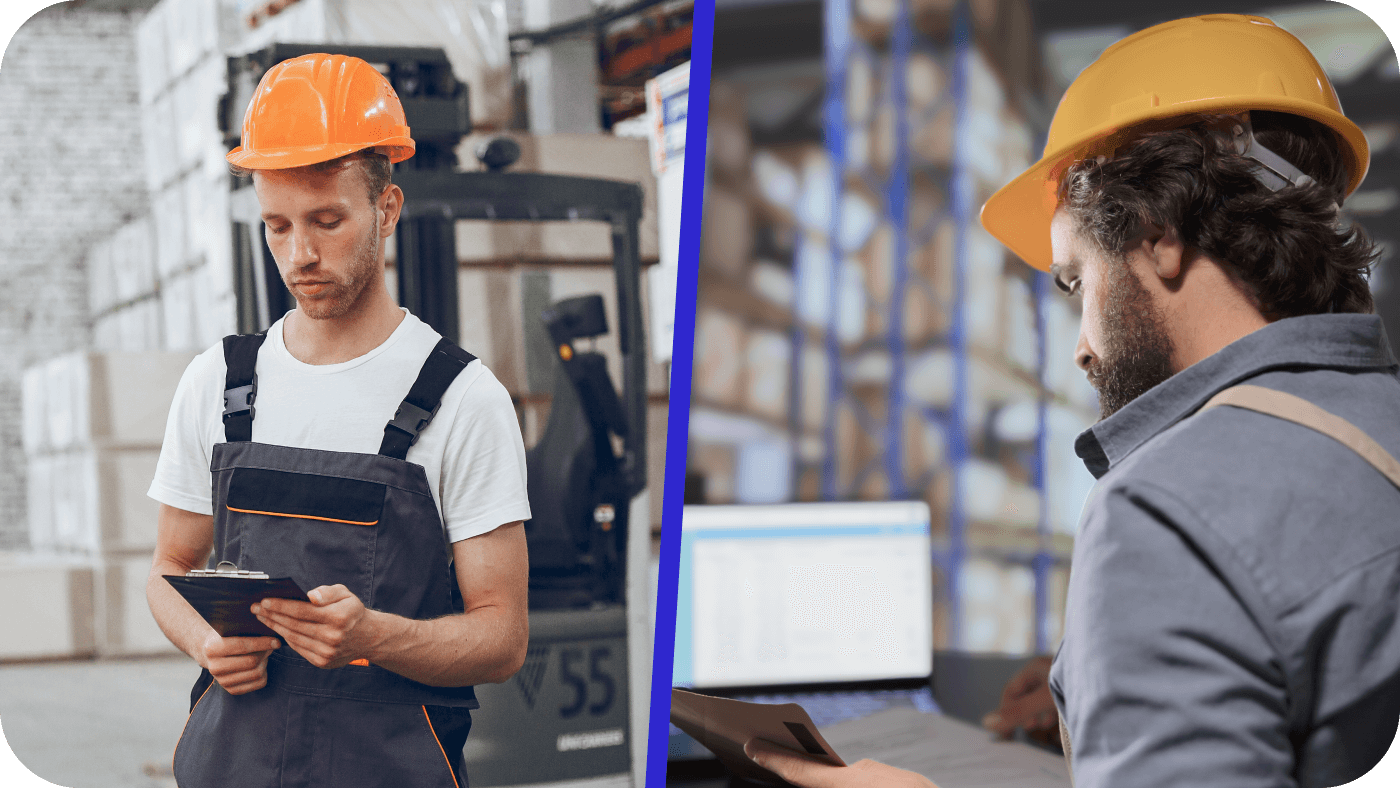
After the system was implemented, downtime due to tool unavailability was significantly reduced. Crews could easily access the necessary equipment from nearby teams, improving workflow efficiency and cutting logistics costs related to transporting tools across sites.
Book a demoBenefits for clients
Reduced downtime
Quick access to tools from neighboring crews allowed workers to maintain productivity, minimizing project delays.
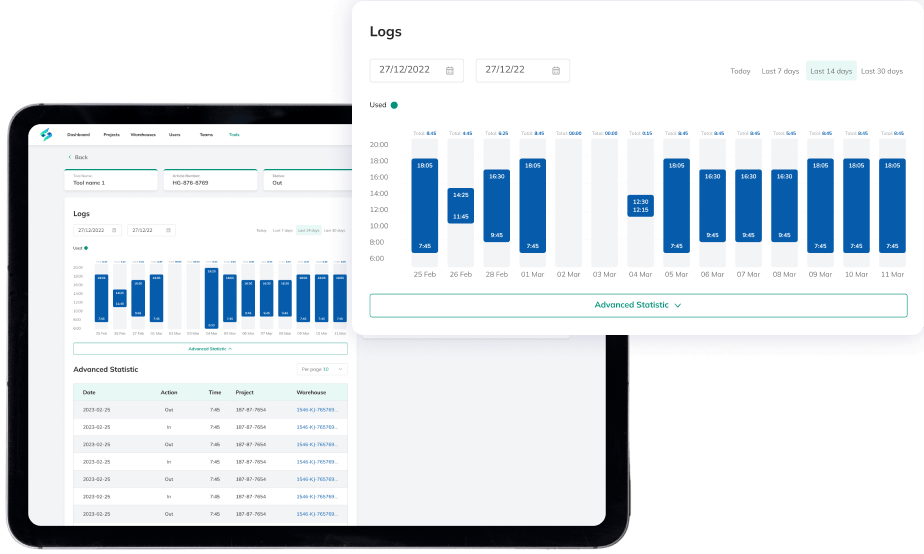
Cost savings
Reduced tool losses and improved warehouse logistics helped minimize the need for frequent tool replacements, with estimated savings of €90,000 per year.
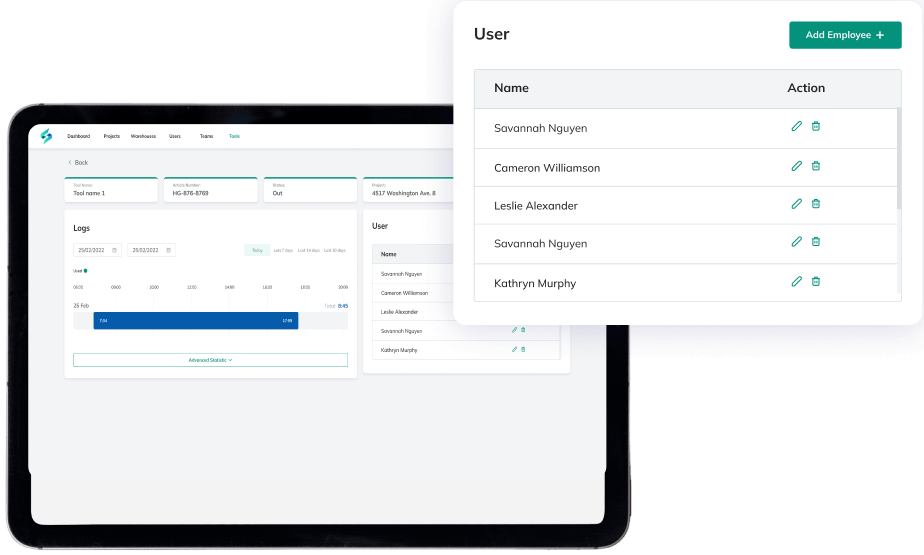